How to Integrate AI in Manufacturing Processes
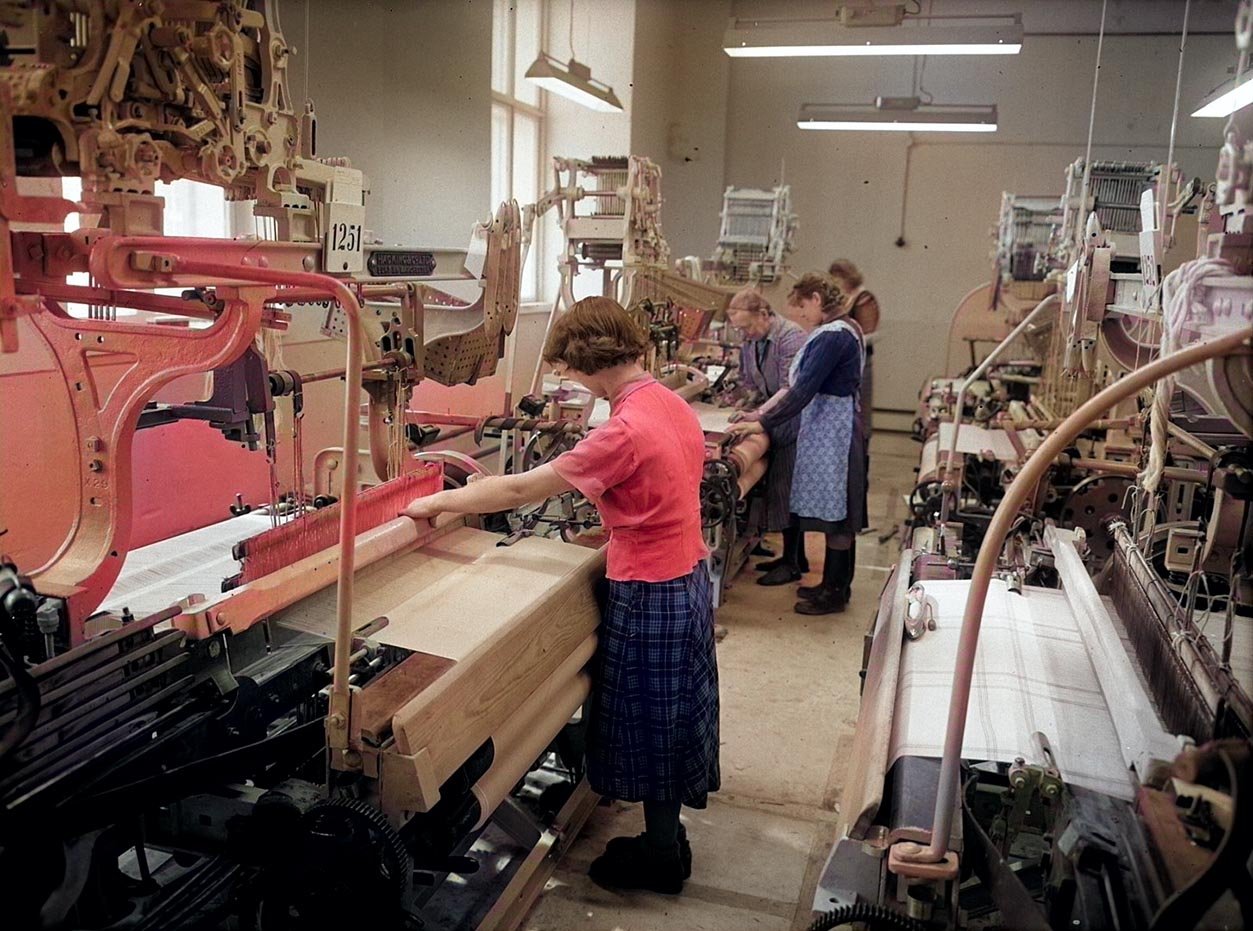
AI in Manufacturing Processes
Artificial Intelligence (AI) has emerged as a transformative force in modern manufacturing, offering innovative solutions to enhance efficiency, reduce costs, and improve product quality. The integration of AI into manufacturing processes enables companies to automate tasks, optimize production lines, and predict equipment failures before they occur. However, the successful implementation of AI in manufacturing requires strategic planning, investment in the right technologies, and a deep understanding of how AI can be leveraged effectively.
This comprehensive guide explores the various ways AI can be integrated into manufacturing, its benefits, challenges, and a step-by-step approach for successful adoption.
Benefits of AI in Manufacturing
Before delving into the implementation process, it is essential to understand the advantages AI offers in manufacturing:
- Enhanced Efficiency – AI-driven automation reduces manual labor, speeds up production, and minimizes human errors.
- Predictive Maintenance – AI-powered sensors can predict machinery failures and alert maintenance teams before breakdowns occur.
- Improved Quality Control – AI-based visual inspection detects defects more accurately than human inspectors.
- Supply Chain Optimization – AI algorithms analyze demand patterns and optimize inventory management.
- Cost Reduction – AI helps in reducing operational costs through automation, predictive analytics, and waste minimization.
- Worker Safety – AI-driven robotics can handle hazardous tasks, reducing the risk of workplace injuries.
- Data-Driven Decision Making – AI provides real-time insights into production performance, helping managers make informed decisions.
Key AI Technologies in Manufacturing
1. Machine Learning (ML)
ML enables systems to learn from data and improve performance over time. In manufacturing, ML can be used for predictive maintenance, quality control, and process optimization.
2. Computer Vision
AI-powered computer vision systems inspect products for defects, ensuring higher quality standards and reducing waste.
3. Industrial Robotics
AI-powered robots perform tasks such as assembly, welding, and packaging with precision and speed, improving production efficiency.
4. Digital Twins
A digital twin is a virtual replica of a physical manufacturing process or product. AI-powered digital twins simulate production scenarios to optimize performance.
5. Natural Language Processing (NLP)
NLP enables AI systems to understand and respond to human commands, improving communication between workers and automated systems.
6. Internet of Things (IoT) and AI Integration
IoT sensors collect real-time data from machinery, which AI systems analyze to optimize production and predict maintenance needs.
Steps to Integrate AI in Manufacturing
1. Assess Business Needs and Objectives
Before implementing AI, manufacturers must identify specific challenges they want to address. Common objectives include improving quality control, reducing downtime, and optimizing supply chains.
2. Collect and Analyze Data
AI systems rely on high-quality data for effective decision-making. Manufacturers should gather data from various sources, such as IoT sensors, production logs, and enterprise resource planning (ERP) systems.
3. Choose the Right AI Technologies
Based on the business needs, select appropriate AI technologies such as ML, computer vision, or predictive analytics to address specific challenges.
4. Invest in Infrastructure
Implementing AI requires robust computational infrastructure, including cloud computing, edge computing, and data storage solutions.
5. Develop AI Models and Algorithms
AI models must be trained using historical data to recognize patterns, predict failures, and optimize processes. Collaboration with AI experts or hiring data scientists can accelerate this process.
6. Pilot Testing
Before full-scale deployment, conduct pilot tests to evaluate AI performance in real-world manufacturing settings. Identify potential challenges and fine-tune the AI models accordingly.
7. Integrate AI with Existing Systems
AI solutions must seamlessly integrate with existing manufacturing execution systems (MES) and ERP platforms to ensure smooth operations.
8. Train Employees
Successful AI implementation requires workforce training. Employees should understand how AI tools work and how to interpret AI-driven insights.
9. Monitor and Optimize
Post-implementation, AI systems should be continuously monitored to ensure they deliver the expected benefits. AI models may require periodic updates to adapt to changing production conditions.
10. Scale AI Implementation
Once AI solutions demonstrate value in pilot projects, they can be scaled across different manufacturing processes and production facilities.
Challenges of AI Integration in Manufacturing
Despite its numerous benefits, integrating AI in manufacturing comes with challenges:
- High Initial Investment – AI adoption requires significant capital investment in hardware, software, and workforce training.
- Data Quality Issues – AI relies on large datasets, and poor data quality can lead to inaccurate predictions.
- Cybersecurity Risks – AI-driven systems are susceptible to cyber threats, requiring robust security measures.
- Workforce Resistance – Employees may fear job displacement due to automation, necessitating change management strategies.
- Complexity in Implementation – AI integration involves compatibility challenges with existing systems.
- Regulatory Compliance – AI-driven manufacturing must comply with industry regulations and data protection laws.
Future of AI in Manufacturing
The future of AI in manufacturing is promising, with emerging trends set to revolutionize the industry:
- Autonomous Factories – Fully AI-driven smart factories with minimal human intervention.
- Collaborative Robotics (Cobots) – AI-powered robots working alongside humans to enhance productivity.
- AI-Driven Sustainability – AI optimizing energy consumption and reducing waste to promote green manufacturing.
- Advanced AI Predictive Analytics – Enhanced predictive maintenance models to further reduce downtime.
- Blockchain and AI Integration – AI enhancing transparency and security in supply chains through blockchain technology.
Integrating AI in manufacturing processes is no longer a futuristic concept but a necessity for companies looking to stay competitive in the Industry 4.0 era. By leveraging AI technologies such as ML, computer vision, and IoT integration, manufacturers can enhance efficiency, reduce costs, and improve product quality.
However, AI adoption requires a well-planned approach, including assessing business needs, investing in infrastructure, and training employees. While challenges exist, companies that successfully navigate AI implementation will position themselves as industry leaders in the future of manufacturing.
By embracing AI, manufacturers can drive innovation, optimize production, and create a smarter, more sustainable industrial landscape. image/wikipedia modified